Fastener Selection Guide: Best Options for Dry Environments
Understand fasteners for dry environments
Select the right fastener for a dry environment require careful consideration of various factors include material properties, corrosion resistance, and application requirements. Dry environments will present unique challenges that will differ importantly from humid or wet conditions, will influence which fastener types will perform optimally.
Dry environments typically have low humidity levels, minimal moisture exposure, and oftentimes experience temperature fluctuations. These conditions affect how fasteners perform over time and can impact their longevity and reliability.
Key considerations for fastener selection
Before identify specific fastener types, understand the critical factors that influence performance in dry settings is essential:
Material properties
The material composition of a fastener importantly affect its performance in dry conditions. Different metals and alloys respond otherwise to low humidity and temperature variations.
In dry environments, materials that might commonly require moisture for protective oxide formation may behave otherwise. For instance, some stainless steels rely on moisture to maintain their passive oxide layer, which can be compromise in exceedingly dry conditions.
Thermal expansion
Dry environments oftentimes experience significant temperature fluctuations between day and night or seasonal changes. These fluctuations cause materials to expand and contract, potentially loosen fasteners over time.
Fasteners with similar thermal expansion coefficients to the materials they’re will join will maintain better connection integrity during temperature changes. This matching help prevent loosening cycles that can lead to fastener failure.
Dust and particulate considerations
Many dry environments contain airborne dust and particulates that can interfere with thread connections or move parts. These particles can accelerate wear through abrasion or prevent proper fastener seating.
Fasteners design with features that minimize dust intrusion or that can be easy clean perform advantageously in these conditions. Thread designs that resist clogging are specially valuable in dusty environments.
Optimal fastener types for dry environments
Carbon steel fasteners
Carbon steel fasteners offer excellent strength and durability in dry environments. Without moisture to trigger corrosion, these fasteners can maintain their integrity for extended periods. They’re besides cost-effective compare to many alternatives.
For additional protection, carbon steel fasteners can be treated with various coatings:
-
Zinc plating
Provide basic protection against occasional moisture exposure -
Black oxide coating
Offer minimal protection but improve appearance and reduce light reflection -
Phosphate coating
Create a porous surface that retain lubricants wellspring, beneficial in applications with move parts
Carbon steel fasteners are ideal for indoor applications or enclose dry environments where strength is a primary concern and exposure to moisture is minimal.
Aluminum fasteners
Aluminum fasteners offer several advantages in dry environments. They’re lightweight, course corrosion resistant, and don’t require additional protective coatings in virtually dry applications.

Source: lloydsinfrasystems.com
The thermal properties of aluminum make it specially suitable for environments with temperature fluctuations. Aluminum’s high thermal conductivity allow it to distribute heat equally, reduce the risk of localized stress points during temperature changes.
While not ampere strong as steel, aluminum fasteners provide sufficient strength for many applications. They’re usually use in:
- Electronics enclosure
- Aircraft components
- Lightweight structures
- Applications where weight reduction is important
Anodized aluminum fasteners offer enhance surface hardness and wear resistance, make them regular more suitable for dry environments with potential abrasive exposure.
Titanium fasteners
For critical applications in dry environments, titanium fasteners provide exceptional performance. They offer an outstanding strength to weight ratio and natural corrosion resistance without require protective coatings.
Titanium fasteners maintain their mechanical properties across a wide temperature range, make them ideal for dry environments with extreme temperature variations. Their low thermal expansion coefficient help maintain joint integrity during temperature cycling.
While importantly more expensive than steel or aluminum alternatives, titanium fasteners are justified in applications where:
- Weight reduction is critical
- Exceptional strength is required
- Long term reliability justify higher initial costs
- Replacement would be difficult or impossible
Aerospace, medical devices, and high performance automotive applications oftentimes utilize titanium fasteners despite their premium cost.
Self lock fasteners
Dry environments oftentimes experience vibration and thermal cycling that can cause fasteners to loosen over time. Self lock fasteners incorporate features that prevent this loosening without require additional components.
Several self lock designs work advantageously in dry environments:
-
Nylon insert lock nuts
Use a nylon ring that deform slender to create tension against the mating threads -
Distort thread lock nuts
Have slender dedeformedhreads that create friction against the mating threads -
Serrate flange fasteners
Use serrations to bite into the mating surface, prevent rotation -
Prevail torque lock bolts
Have slender dedeformedhreads that create friction
These self lock features are peculiarly valuable in applications subject to vibration or thermal cycling, common challenges in many dry environments.
Thread locking compounds and dry environments
Thread lock compounds provide an additional security measure for fasteners in dry environments. These chemical compounds fill the space between mating threads, harden to prevent loosening.
Different formulations offer vary levels of strength:
-
Low strength compounds
(typically blue )allow for disassembly with hand tools -
Medium strength compounds
Provide greater security while ease allow dismantling with standard tools -
High strength compounds
(typically red )create permanent bonds that require heat for dismantling
In dry environments, thread lock compounds can compensate for the absence of moisture that might differently help create natural friction between threads. They besides help seal threads against dust intrusion, a common issue in dry settings.
Specialized fasteners for extreme dry conditions
Desert and arid environment fasteners
Passing dry desert environments present unique challenges include high temperature variations, intense UV exposure, and abrasive sand particles. Fasteners for these conditions require special considerations:
- UV resistant coatings prevent degradation from solar radiation
- Sand resistant thread designs minimize abrasive wear
- Materials with match thermal expansion properties maintain joint integrity during extreme temperature swings
Specialized coatings like ceramic base dry film lubricants can provide farseeing last protection against gall and seize in these harsh conditions.
High temperature dry environments
Some dry environments besides experience high temperatures, such as industrial furnaces, engine compartments, or desert conditions. Fasteners for these applications must maintain their mechanical properties at elevated temperatures.
Suitable options include:
-
Income fasteners
Maintain strength and corrosion resistance at temperatures up to 1800 ° f (982 ° c ) -
High temperature stainless steel alloys
Offer good performance up to 1500 ° f (816 ° c ) -
Ceramic fasteners
Can withstand extreme temperatures but have limited tensile strength
These specialized fasteners oftentimes incorporate designs that accommodate thermal expansion, such as slot holes or Belleville washers, to maintain proper preload across temperature ranges.
Application specific recommendations
Electronics and low humidity environments
Electronic equipment oftentimes operate in control, low humidity environments. Fasteners for these applications must avoid generate particles or dust that could interfere with sensitive components.
Recommend fasteners include:
- Stainless steel machine screws with roll threads that produce minimal particulates
- Aluminum fasteners for applications require non-magnetic properties
- Captive screws that prevent fastener loss inside sensitive equipment
For electronics applications, fasteners with precision machine threads minimize the risk of particulate generation and provide consistent torque values for reliable assembly.
Structural applications in dry climates
Structural fasteners in dry climates must maintain long term integrity despite temperature cycling and potential seismic activity. High strength structural bolts with appropriate preload are essential for these applications.
Key considerations include:

Source: compasssunrooms.com
- Proper torque specifications to achieve optimal preload
- Direct tension indicators to verify correct installation
- Regular inspection schedules to identify any loosening
- Consideration of thermal expansion effects on joint integrity
For critical structural applications, tension control bolts (tTCbolts )provide visual confirmation of proper installation and help ensure consistent preload across multiple fasteners.
Installation best practices for dry environments
Proper installation techniques are crucial for fastener performance in dry environments:
Surface preparation
Clean, debris free surfaces ensure proper fastener seating and load distribution. In dry environments, static electricity can cause dust to cling to surfaces, require thorough cleaning before fastener installation.
Anti-static tools and cleaning methods can minimize this issue, especially in electronics applications or environments with combustible dust.
Torque specifications
Dry environments oftentimes require specific torque values that differ from standard recommendations. Without the natural lubrication provide by humidity, thread friction can increase, potentially lead to inaccurate preload or fastener damage.
Use appropriate lubricants or adjust torque specifications can compensate for these dry conditions. Invariably consult manufacturer recommendations for dry environment applications.
Regular inspection
Regular with optimal fastener selection, regular inspection remain important in dry environments. Look for:
- Signs of loosen due to thermal cycling
- Dust accumulation that might interfere with fastener function
- Wear patterns indicate potential future failure points
- Evidence of material fatigue or stress crack
Establish a regular inspection schedule helps identify potential issues before they lead to fastener failure or structural compromise.
Conclusion
Select the optimal fastener for dry environments require balance multiple factors include material properties, application requirements, and environmental conditions. While carbon steel fasteners provide cost-effective solutions for many applications, aluminum and titanium alternatives offer advantages in specific scenarios.
Self lock fasteners and thread lock compounds provide additional security against loosen in vibration prone or thermally cycle environments. For extreme conditions, specialized fasteners with appropriate coatings or material compositions ensure long term performance.
By cautiously consider the specific requirements of your application and the characteristics of the dry environment, you can select fasteners that provide optimal performance, reliability, and longevity. Remember that proper installation techniques and regular inspection remain crucial components of any fasten system, disregarding of environmental conditions.
MORE FROM getscholarships.de
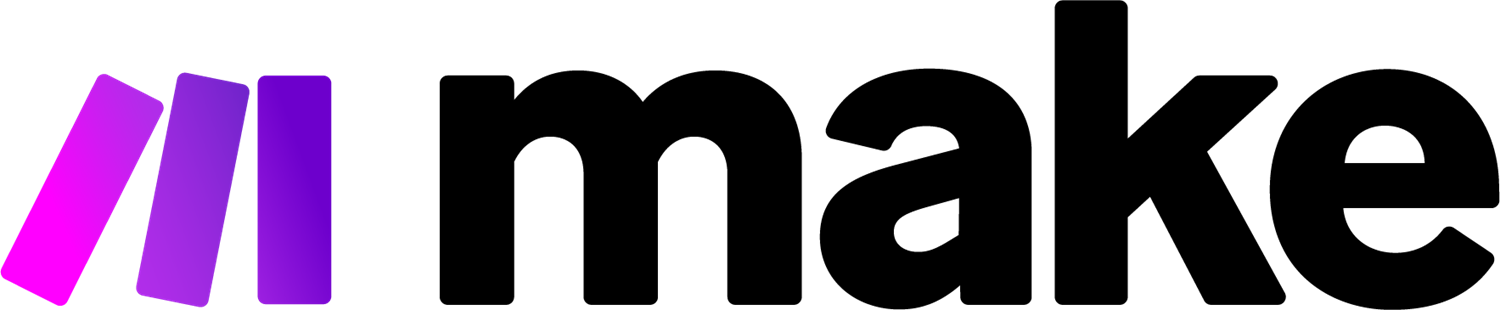

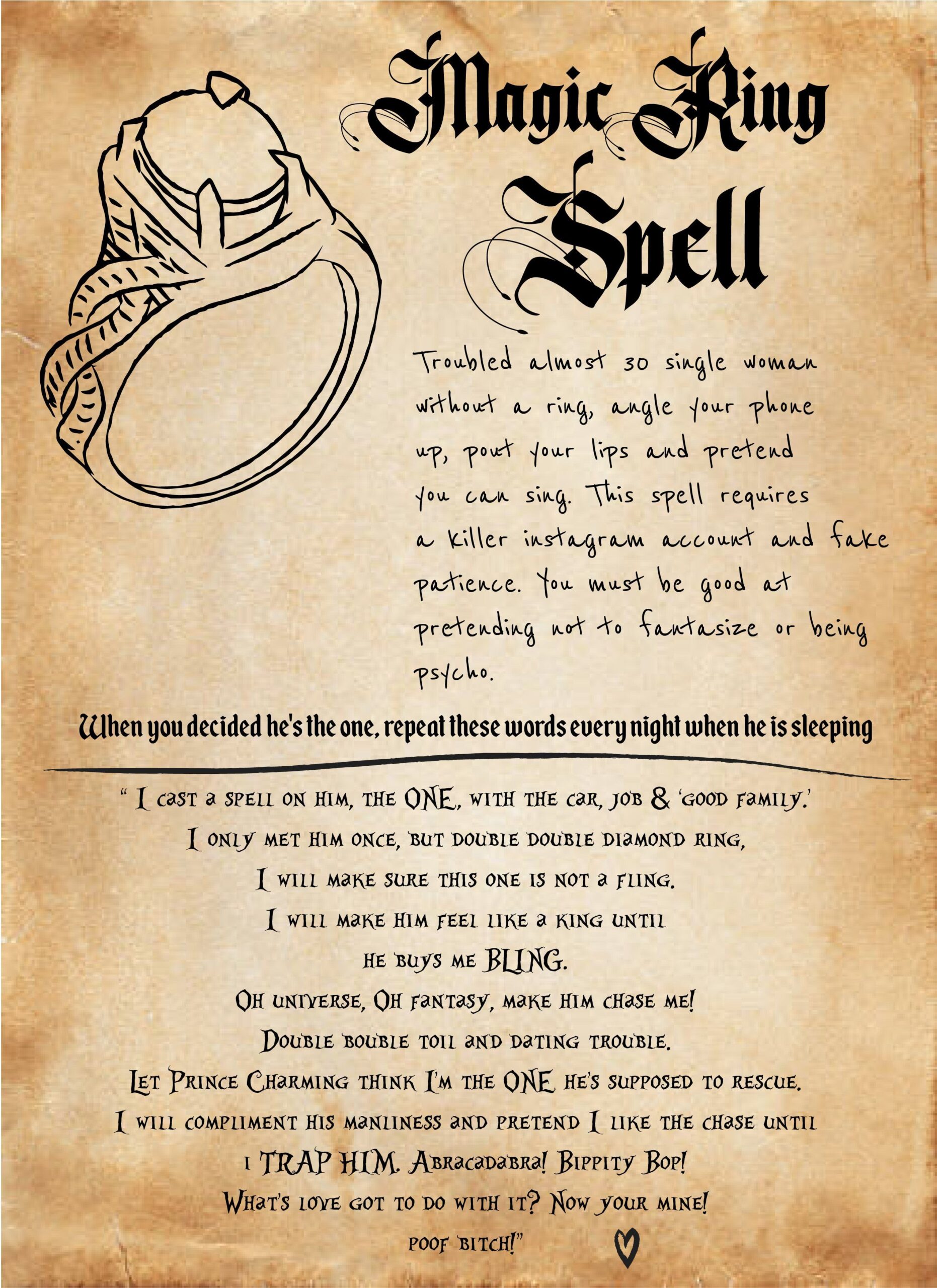
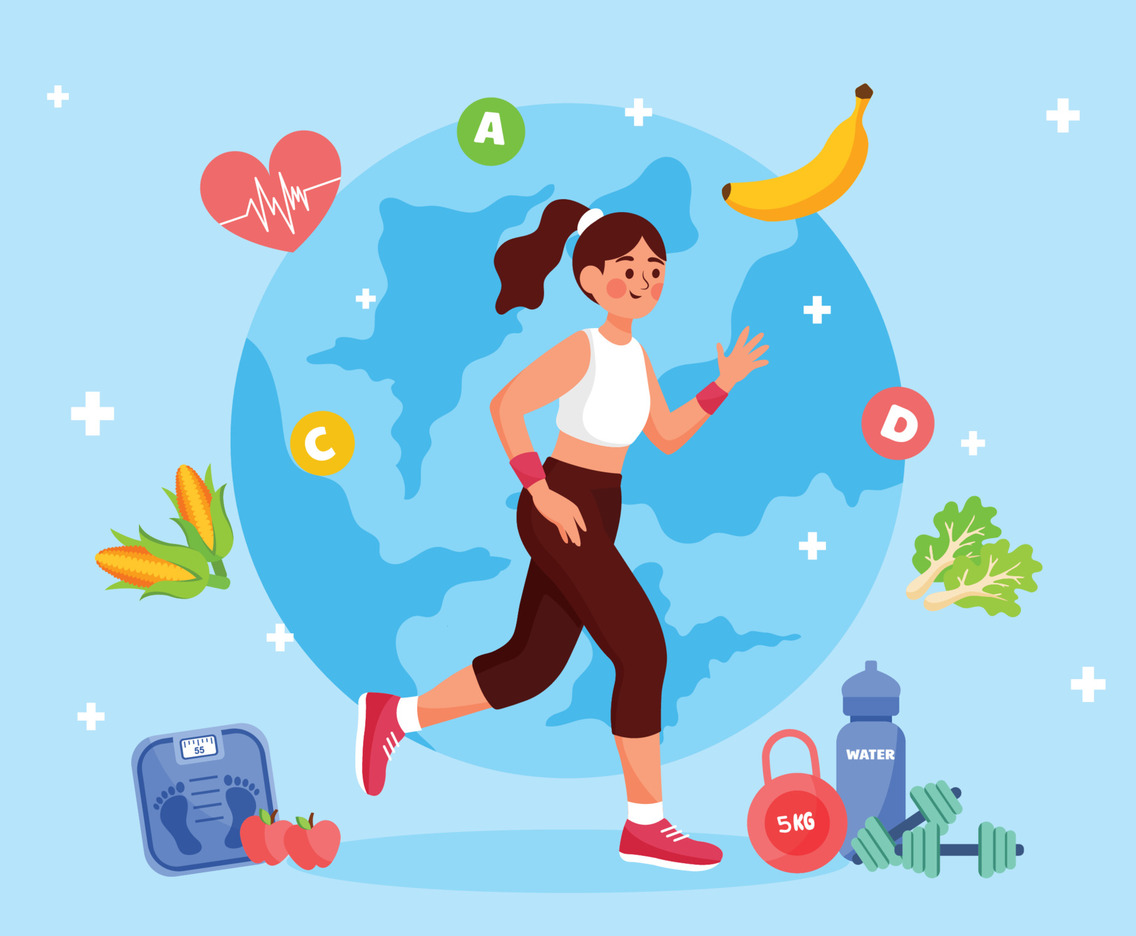
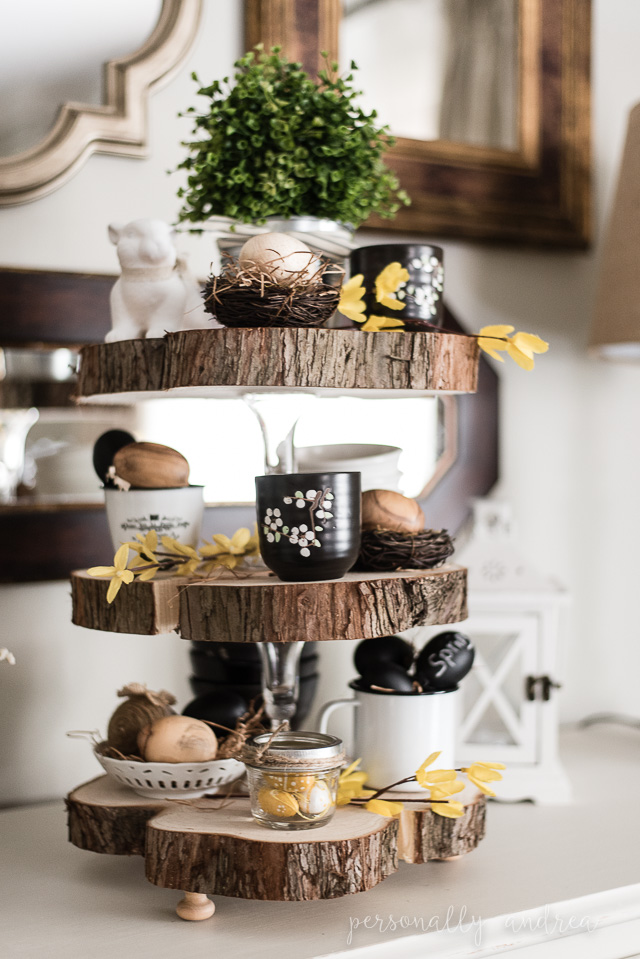
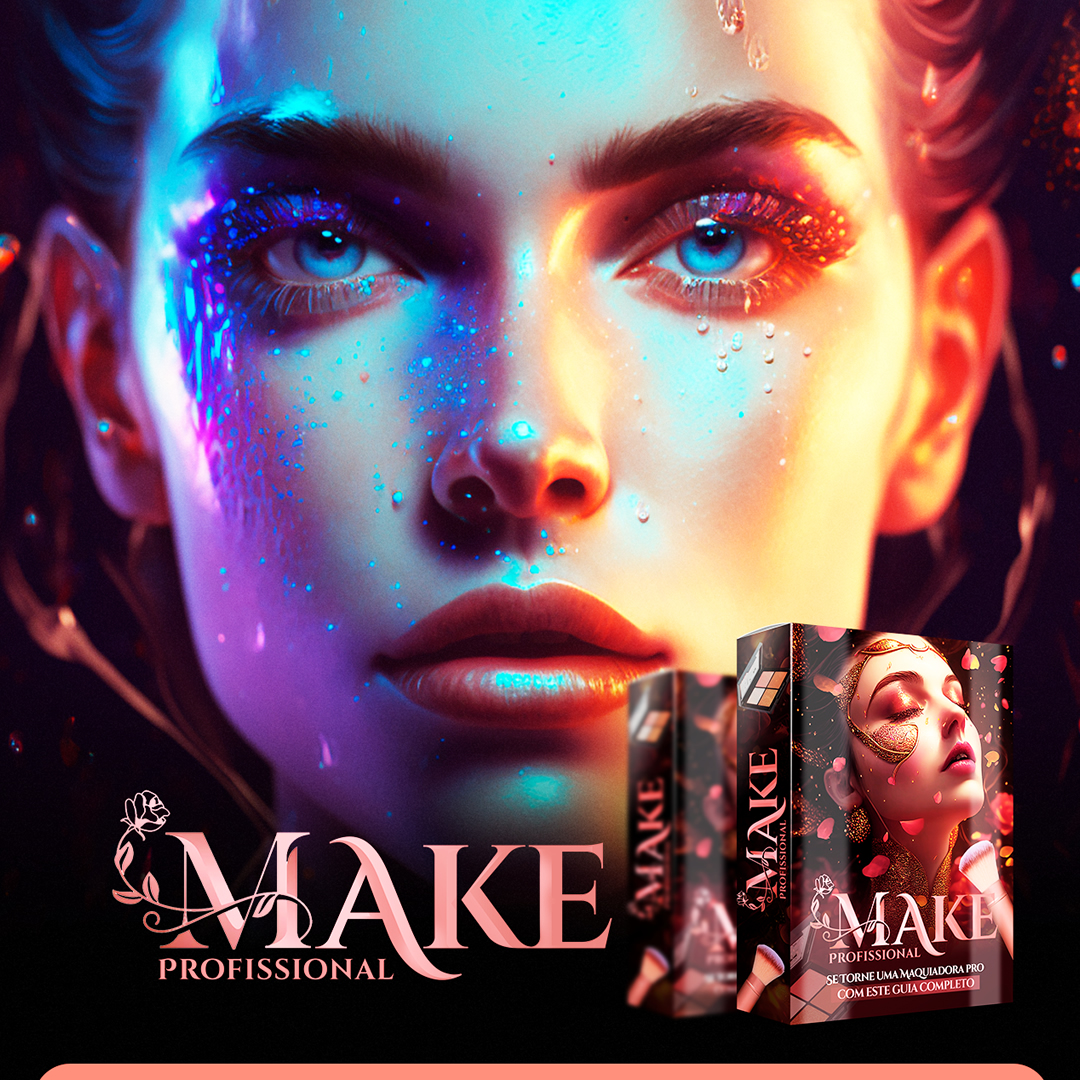
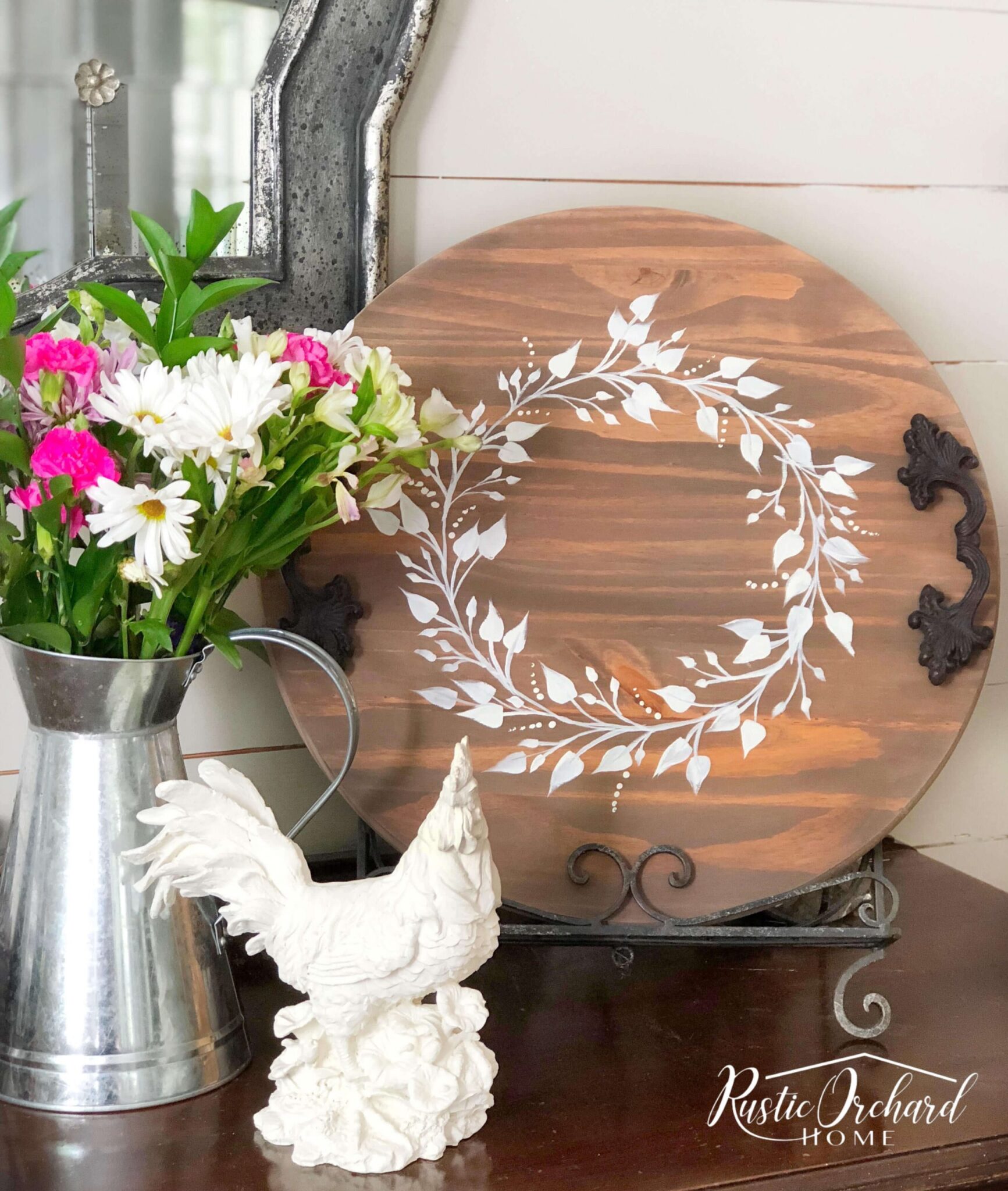
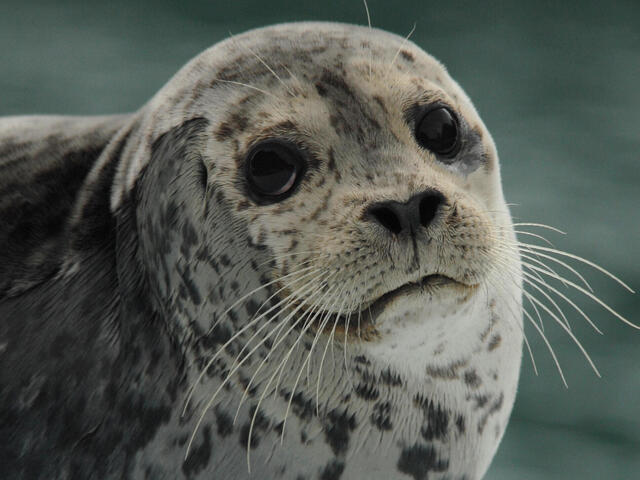
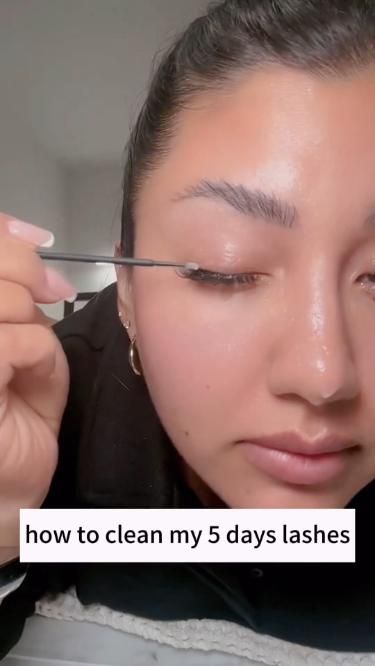
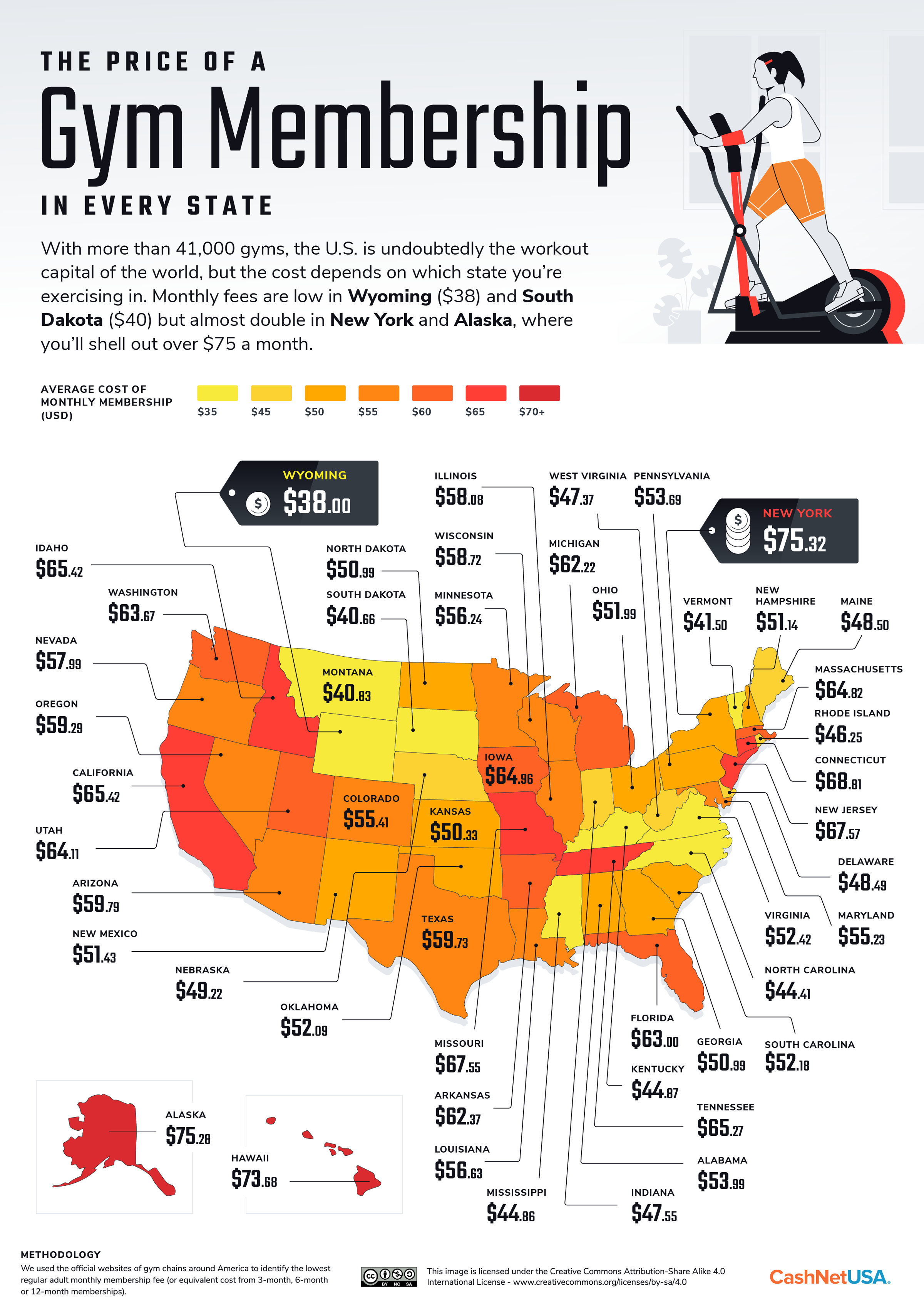
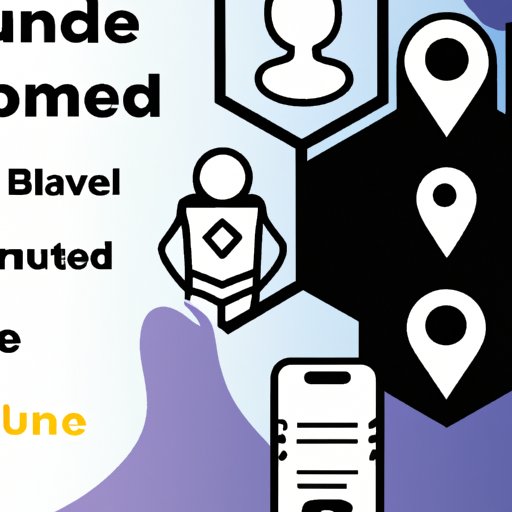
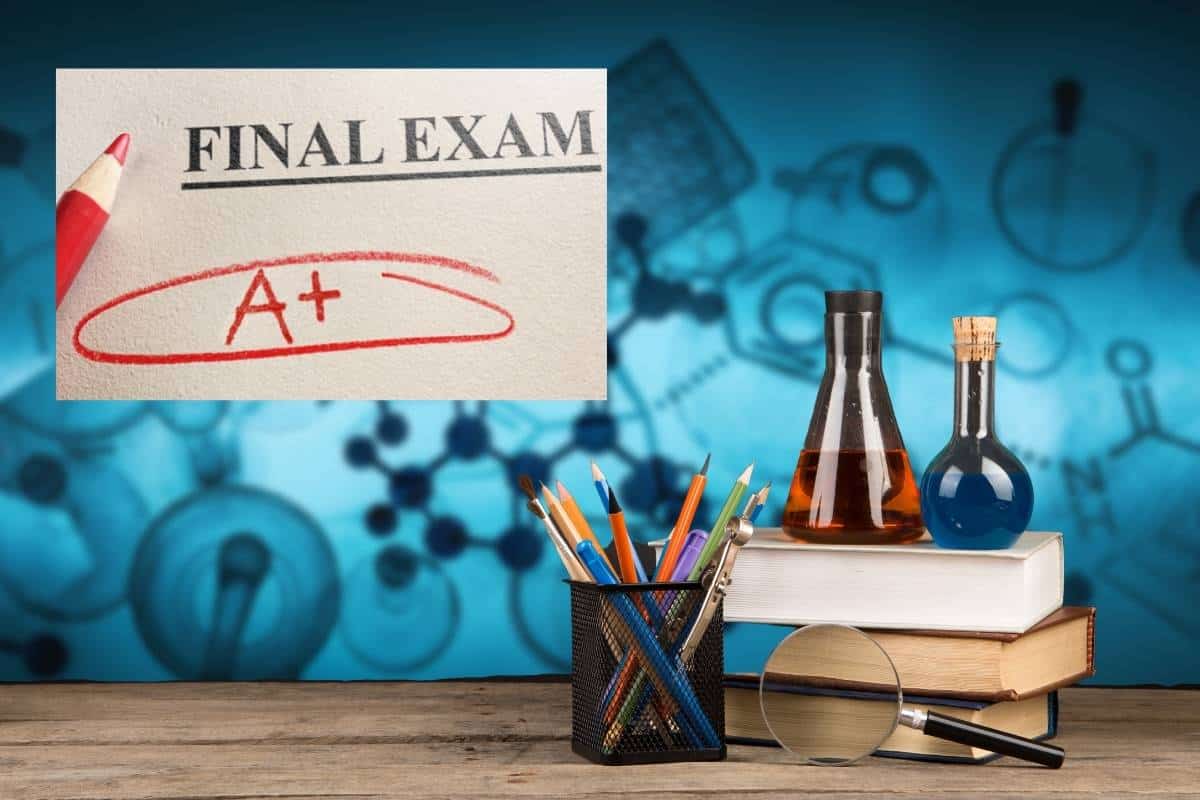